BIM & VDC
Leveraging BIM with Vitalant
Over the last several decades, Dome has utilized Building Information Modeling (BIM) to understand how we are approaching the execution of complex projects by generating a virtual view.
We are excited to share how Dome approaches and completes high-profile, complex projects led by our BIM Department. To get a better understanding of the BIM/Vitalant partnership, we sat down with John Mack, VDC/BIM Manager, Michael Conlon, VDC Project Manager, and the Vitalant Project Team, Juan Restrepo, Project Manager, and Skip Michaud, Superintendent.
What is BIM?
Building Information Modeling, or BIM, refers to the digital representation of a facility’s physical and functional characteristics. This shared resource has two main functions, creating 3D objects and creating associated data of the object. Please see the images provided for a sample of a Building Information Model (Left) and its current progress at the Vitalant Research Institute project (Right).
BIM also enables Virtual Design and Construction, or VDC, which is the management of the models. We use VDC as a visual management method with BIM for construction analysis and work processes. John Mack always says, think the of as BIM as the noun and VCD as the verb.
Why use BIM?
Leaning on our BIM tools during the preconstruction phase produces impressive impacts on the overall project. BIM allows us to discover design issues up front, leaving less room for adjustments down the road. Having this increased visibility during the preconstruction phase allows for improved design, accurate construction planning, visibility into a predictable cost, and team collaboration.
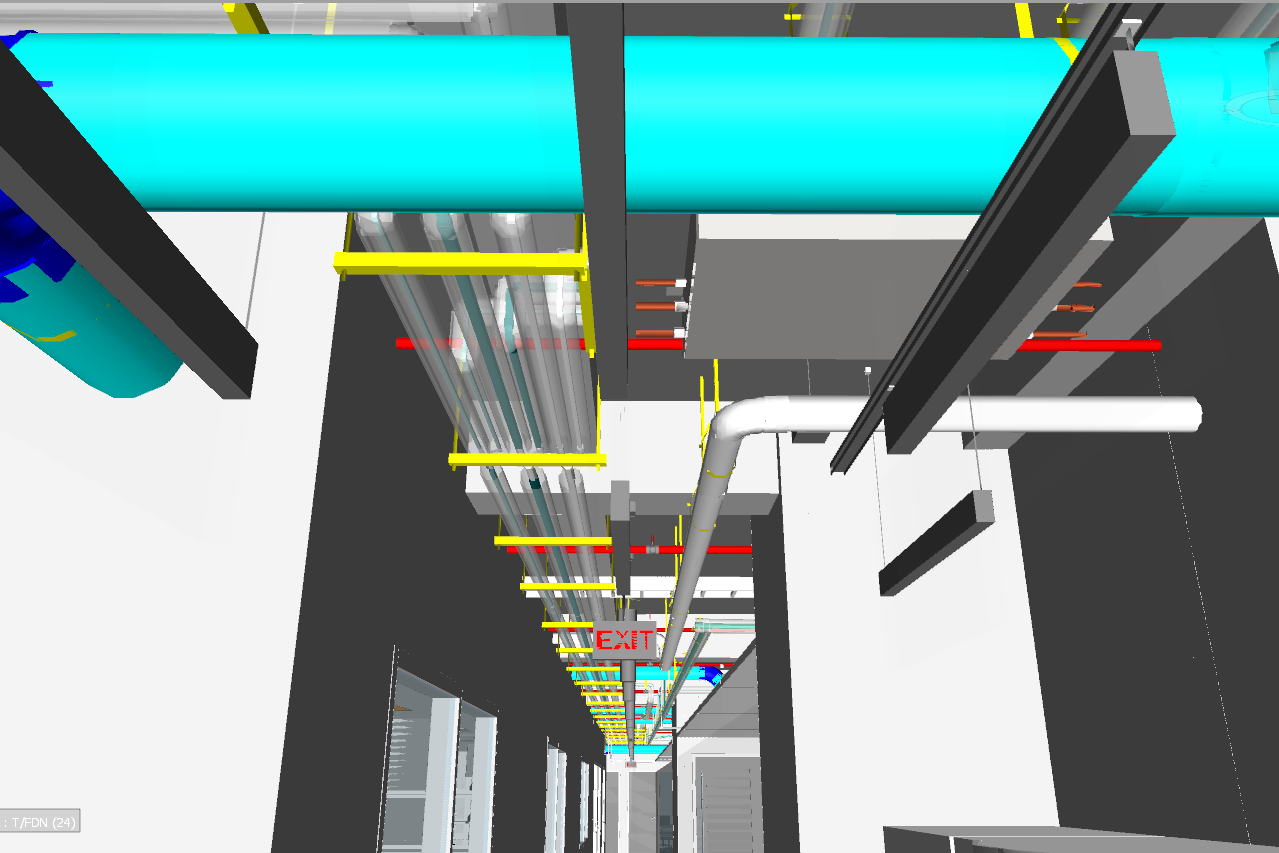
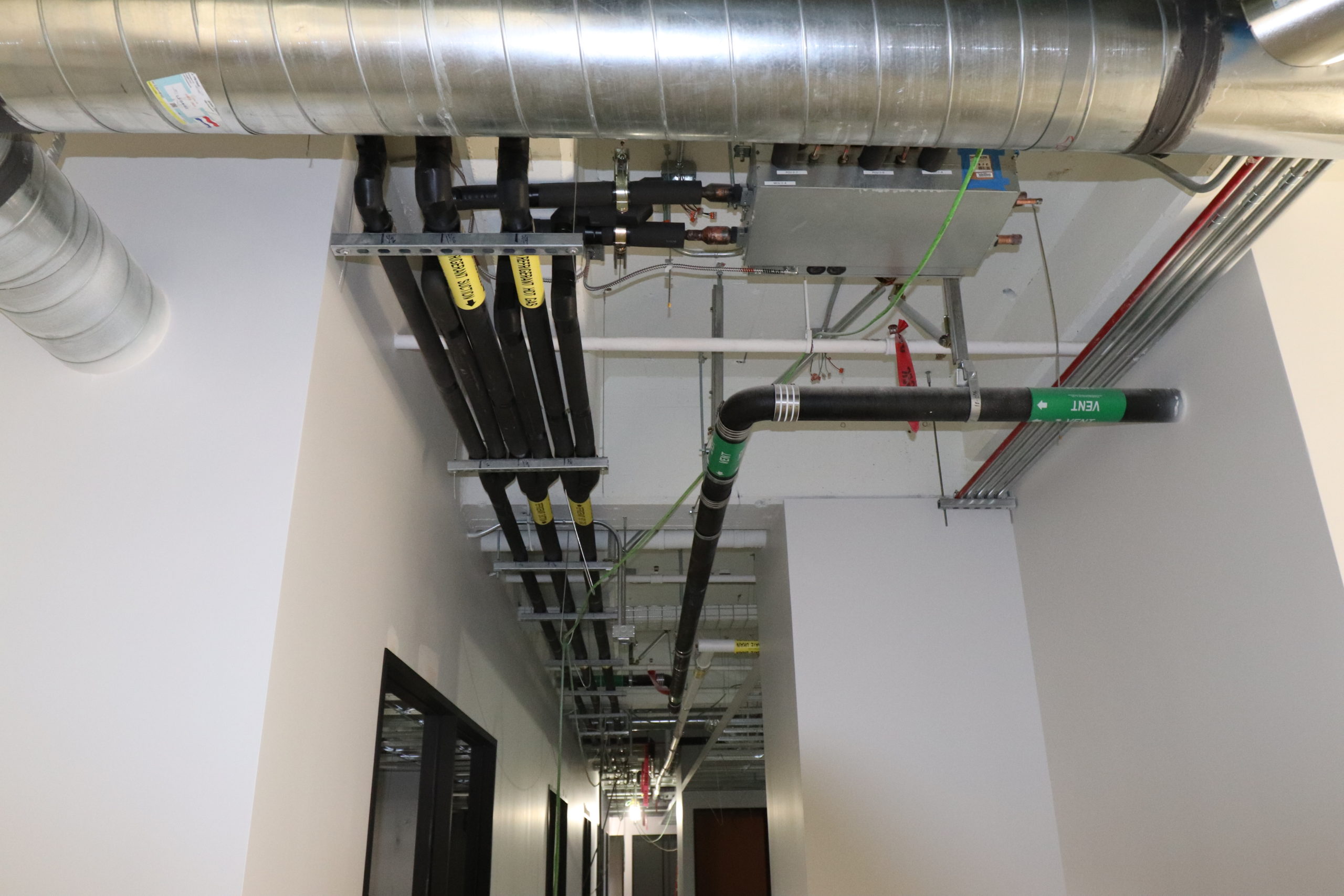
Our BIM Department
For any project looking to add BIM to their project, John Mack, longtime BIM guru and BIM Department Manager, and Michael Conlon, BIM Project Manager work together to ensure a successful BIM process is put in place.
John assigns the BIM lead to the job, provides oversight, and steps into mentor or train when needed, while Michael facilitates and coordinates the BIM process from start to finish. This stellar BIM team is also joined by David Francis, BIM Project Manager, Li Jiang, Sr. Project Engineer, and Jerrod Patton, Project Coordinator.
What are the costs of BIM?
Our first question for the BIM team was understanding the cost of using BIM on a project. John addressed the pricing of our services by sharing, “the deciding factors that weigh into overall cost are the project size, type, complexity, the accuracy of design models, and trade partners selected. We have not found a one size fits all overall cost of BIM on projects“. Using BIM allows our team to catch any design issues that may exist. When we can get ahead of those challenges before construction begins, we can deliver cost savings to the entire team. John elaborates, “what BIM does, is help set cost certainty sooner in the project by allowing the team to plan their work for prefabrication and installation. Using BIM also allows for more confidence in prefabrication, which ultimately leads to schedule savings.“ Michael also shared, “BIM is more than just saving cost. It‘s also a huge time saver for installation, which translates to an increased profit for our clients”.
Are there any risks involved with BIM?
John shared that doing BIM too early is a risk because any BIM performed before the design is fully approved has the potential of rework (which can be costly and affect the schedule). NOT allowing proper time in the schedule to do BIM can also lead to our teams having incorrect design models to coordinate, which leads to rework. Bad BIM is worse than no BIM, and at Dome, we have a culture of Doing it Right.
What challenges has the VDC team faced when using BIM?
A challenge to consider when using BIM is the hurdle and added cost of coordinating the BIM process with our subcontractors. John shared that “some trade partners will upcharge for BIM (electrical and fire protection), while some companies upcharge for not doing BIM (mechanical and plumbing).”
Receiving design models that do not match existing conditions is one of the most common issues John and his team run into. However, John shared, “laser Scanning and Variance Reports allow for improvements to this issue.” Michael leaned into this concept, sharing that laser scans on Tenant Improvement projects are imperative. “When these scans and variance reports are unavailable, it’s hard to identify obstacles in the field.” To alleviate this problem, the Dome VDC team is on a mission to get more laser scans completed in the future, resulting in a better outcome when it comes time to install.
Why aren't more projects using BIM?
For Michael, a problem he‘s run into is persuading project managers that the upfront costs associated with BIM are less than the cost of the problems the team would run into had they not used BIM. BIM gives our team the insight to solve the problems in the field early on. “Providing cost and schedule certainty sooner is the best way to position BIM,” shares John. He continued, “adding BIM is like having an insurance policy where the costs need to be shifted forward in the project, to reduce the chance of having an impactful issue during construction.“
Why should more projects use BIM?
If we can find the issue in BIM, it is less costly to correct than if we caught the issue during the installation/construction of the project. While BIM is not a 100% guarantee we find all the issues, John shares, “I believe it puts us in the 90% range for finding potential problems.” We cannot wholly guarantee that all constructability issues will be caught because not everything is added to the BIM – only the higher impact potential items are modeled.
Michael expanded on this expressing that, “spending more upfront will exceptionally save costs in the field and can help create a schedule that will be as accurate as possible.”
To any team who may be unsure about the benefits of using BIM on their project, the Dome VDC team would like to summarize by sharing, “the cost upfront is pricy but the cost savings for all trade partners to get the job done correctly and without incident in a shorter duration is the key.”
Case Study
VDC CASE STUDY: Vitalant
The Dome VDC Team currently manages the VDC efforts with the Vitalant Research Institute (VRI). For a more in-depth understanding of this partnership, we sought additional insight from Juan Restrepo, Project Manager, and Skip Muchad, Superintendent, on this Life Science Lab project.
Vitalant Research Institute is a 33,000 square foot life science project located at 360 Spear Street in San Francisco and began construction in March 2021. This project’s scope includes the installation of BSL-1, 2, and 3 labs, wet-bench research labs, a vivarium, a freezer farm, and a scientific workplace. The original construction schedule accounted for 31 weeks, with 40 days allocated for BIM coordination.
The team outlined 14 goals as aspirations and requirements for the project, of those, the below were identified as top priority.
- Author model to correct level of development for the current phase of the project.
- Enhance design and construction processes through increased transparency, information access, and exchange among the design team and trade partners to ensure cost certainty, schedule certainty, and creative intent with an end goal to improve project delivery.
- Improve BIM/VDC project delivery strategies by gathering metrics throughout the project and by developing lessons learned, as a basis to define BIM/VDC project delivery on future projects.
- Decrease waste by utilizing a virtual building process to simulate design & construction activities.
- Create a standardized data structure that allows data to be reused, and eliminates redundant and conflicting information.
This project team had multiple intended uses for BIM during the preconstruction phase. The first, to create a Model-Based Coordination of MEP systems. Juan shared that he “opted to utilize this approach to mitigate the risk of coordinating in a 100-year-old building that has minimal overhead and shaft space available due to housing data centers.” Next was the focus on MEP Shop Drawing Production. Juan explained that “through the process of Model-Based Coordination, we were able to generate MEP Shop Drawings that would become the prefabrication/spoil drawings for the trades to utilize. Producing these drawings maximized the efficiency of material production in their shops”. Last but not least, Design Constructability Review was also crucial for the team.
“By spending time scanning the building and comparing the scanned information to the architectural model, we were able to validate/determine that the base design was laid out correctly in the building footprint and work with the design team on major discrepancies.”
Having used BIM, the team was able to identify design issues during the preconstruction phase which helped save countless hours and $ 1,000’s in changes. For example, Michael reflects, “One issue we were able to identify in the BIM process utilizing our laser scan. The model provided by the architect had a few areas where the existing walls and columns were showing one location, and by using the laser scan, we were able to identify that the wall was roughly 4′ off from the model – information the laser scan provided.” With those crucial details in mind, the team was able to make corrections in the BIM model instead of discovering this information after the prefab was complete and sent to the field. Identifying this item in the BIM process allowed for time and cost savings. See below (right) for the laser scan variance report.
We are thrilled to share about the success of our BIM Team and look forward to sharing more successful BIM partnerships in the future!
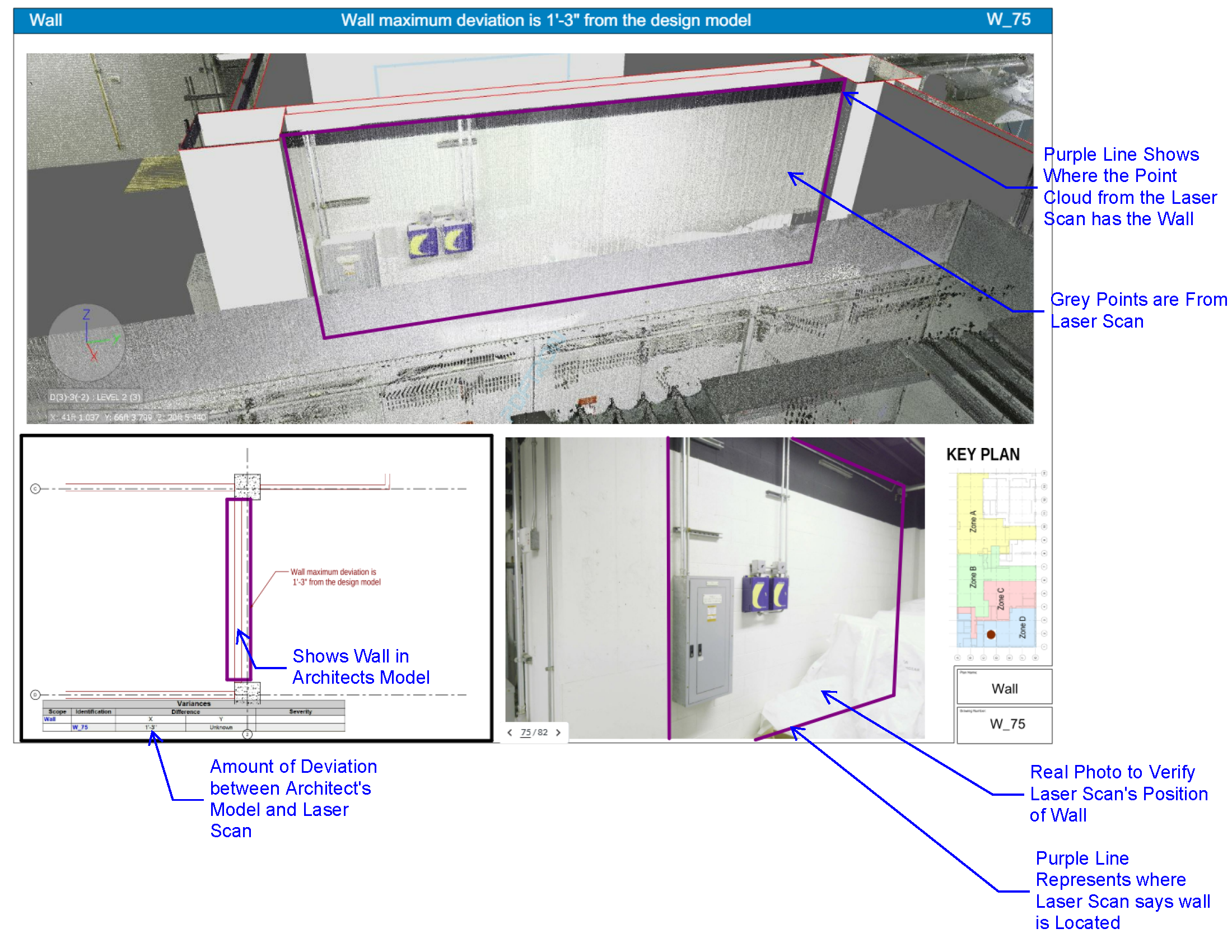